our products and services
Operational excellence
Total quality in our activities
To ensure quality and excellence in its products and services, Avibras strategy is to work in an increasingly integrated and planned manner, driving synergy between its different projects to optimize time and resources. The goal is to fulfill customers' needs and exceed their expectations by boosting efficiency and delivery capacity without sacrificing the company's high standards of quality.
This strategy is supported by a quality engineering structure which includes laboratories and equipment rarely found in a single location in Latin America, as well as the services of some of the main specialists in the market.
Lorena Unit
The Lorena unit, known as Installation 3, produces ammonium perchlorate (AP), an oxidizing material that supplies the oxygen for burning the propellant used in rockets. This is an input whose sale is restricted on the international market, the reason for which the company opted to produce it internally. This verticalization minimizes the risk of potential embargoes on acquiring the product.
Occupying 9 million square meters, the plant was designed to ensure maximum operational safety levels due to the possibility of combustion. It contains contention cells and a fire-fighting system.
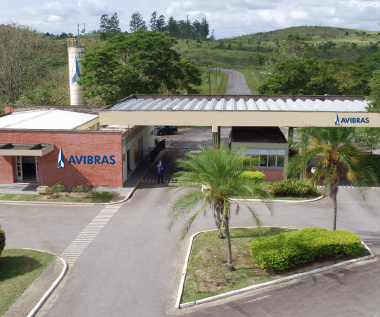
Lorena Unit
The unit is staffed by approximately 90 employees.
Jacareí Unit
Installation 2 houses a major part of Avibras's industrial capacity. It comprises dozens of plants manned by up to 4,500 employees, working three shifts.
The areas include: engineering, mechanical and chemical manufacturing, composite materials, manufacture of rocket and missile launch containers, surface treatment (KTL), quality laboratories, X-ray inspection, commercial and administrative offices, as well as the RPA (Remotely Piloted Aircraft) manufacturing area, testing benches (rocket and combustion engines and turbines), a special vehicle testing ground and armament bunkers.
In 2014, the Jacareí installation inaugurated its armored vehicle plant, considered to be the most modern in Brazil. In an area of 18,000 square meters, the industrial complex has boosted the company's production and technological capacity while reducing costs.
The bold, innovative design enabled the complex to centralize all industrial operations, providing expanded infrastructure to meet Brazilian and overseas demand. Production is currently around
100 vehicles per year.
The plant comprises the following areas: Special Vehicle Manufacturing (Mechanics, Electronics and Integration; Vehicle Design and Engineering; Technical Documentation; Quality Assurance, Inert and Chemical Materials Storage Areas. The new plant also houses the Customer Support Department, with training areas for customers.
Focused on sustainability, the installations were designed with roofing that permits natural lighting and thermal insulation to ensure greater comfort for employees. LED lights were also installed, resulting in significant energy savings.
The design incorporated facilities for harvesting rainwater, which is used in the gardens and toilets, reducing overall water consumption.
The installation of the operations in a single location drives operational gains, with the reduction of logistics costs and increased productivity due to optimized process flows.
The inauguration of the plant led to the beginning of the implantation of AS9100, the international quality management standard for the Aeronautics, Space and Defense industry.
This certification is important because it shows the company has the capacity to fulfill the needs and requirements of its customers, resulting in greater competitive advantage in the market.
The certification is scheduled to be granted in the second half of 2017.
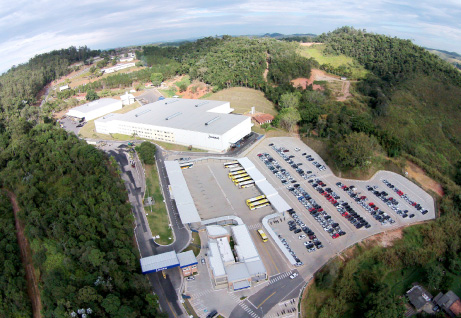
Jacareí Unit houses a major part of Avibras's industrial capacity
Customer satisfaction
G4-PR1, G4-PR2, G4-PR5Avibras evaluates 100 % of the products it acquires and manufactures, at the acquisition and manufacturing (development and production) stages, as well as upon delivery of the end product, ensuring quality and safety for customers.
The degree of defense product customer satisfaction is measured using the customer satisfaction index, the indicator applied to Brazilian customers.
In 2016, we assessed the satisfaction of the company's two active clients, achieving an average satisfaction rate of 87.5%.
Another result arising from this work is the inexistence of recorded cases of non-compliance with regulations and voluntary codes related to impacts on customers caused by products and services.
Customer Support
We build and cultivate long-term relationships with our customers through the provision of complete Integrated Logistic Support. Our highly specialized work force is fully focused on the customer. This program encompasses training, technical support, the supply of simulators, equipment, replacement parts and special tools.
Certifications
GRI G4-15
Avibras is certified in surface treatment production areas in accordance with the international ISO 9001 standard. The company has armed forces Allied Quality Assurance Publication AQAP – 2110 certification, covering defense system design, development, manufacture, integration and technical assistance, key recognition of the company's quality system for the provision of services in the aerospace sector.
The standard is employed by the member nations of the North Atlantic Treaty Organization (NATO) to ensure quality during the full life cycle of product, service and defense system processes.
Avibras also has Brazilian Army certification in the INAvEx 1005 standard: Assessment and Qualification of Companies and Civil and Military Organizations for the execution of maintenance services for the Army Aviation wing.