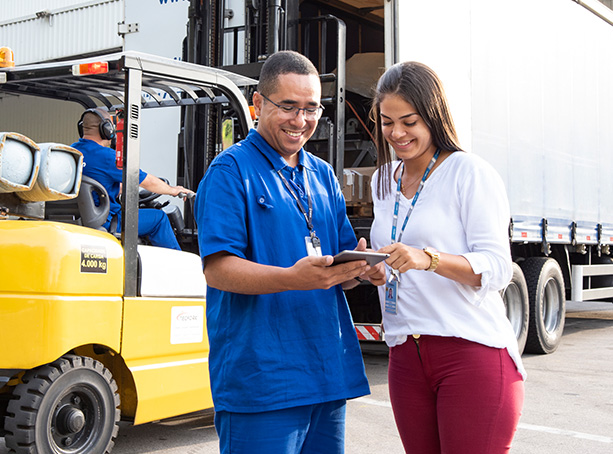
During 2018, a quality assurance approach was adopted, ensuring that quality requirements are monitored from the sourcing of a raw material or service from a supplier right through to the delivery of end products to clients. To make this happen, the supplier management and qualification process was reinforced with specialists from the engineering, procurement and quality areas, as a means of checking and monitoring quality, quantities and deadlines in industrial processes. Regarding installed technical capacity, Avibras made significant investments in its test laboratories for the approval, certification and development of products, boosting its capabilities in terms of volume and quantity, as well as improving equipment quality. 416-1
AS9100:D-2016
ISO 9001:2015
AQAP-2110
InAvEx 1005
Avibras has some 500 Brazilian and international suppliers. Approximately, 90% are Brazilian companies located in the state of São Paulo, mainly in the Vale do Paraíba and Greater São Paulo regions. The international suppliers are concentrated in North America, Europe and Asia. The company’s supply chain consists principally of items such as stamped, forged, wrought and machined parts, plastic injected components, boilers, cabling and wiring materials, chemicals and electronic components, as well as services. 102-9
Avibras suppliers are developed in accordance with the PDCA management cycle. After a supplier has been identified, there is a qualification process involving the evaluation of the firm’s installed technical capacity, process and quality indicators, as well as checking its good standing in the market.
The process includes the analysis of documents and inspections of the suppliers’ premises. This is followed by an audit process involving interaction between the company’s engineering, quality and procurement areas and the supplier.
Once past this stage, the provider must supply a test production part, which is evaluated to see if it is compliant with company specifications and requirements. Once a supplier has been approved, Avibras focuses on monitoring and controlling the company’s deliverables to ensure compliance with quality requirements, production volumes and delivery times.
Avibras adopts a supplier qualification process involving the technical evaluation of providers. This is known as the Supplier Conference. It involves the presentation of the challenges the company will face over the coming years and the presentation of the overall results of suppliers’ performance. It also comprises a channel for dialogue by means of which suppliers may communicate their needs, suggestions, criticisms and praise. This process is aimed at forging closer relations between Avibras and suppliers, improving communication and, by extension, driving enhanced results.
The process follows a model developed by Avibras based on global standards, enabling the adjustment and understanding of all the necessary information and requirements including:
Systematization of the identification and development of suppliers.
Continuous improvement in product quality and post-sale support.
Permanent technological evolution.
Total reliability in quality performance and the control of noxious substances with constant monitoring, ensuring that Avibras receives quality assured inputs.
Continuous improvement in productivity and the elimination of waste throughout the value chain, driving ongoing reductions in costs.
Promotion of the use of materials, processes and products whose environmental impact is compliant with the laws in force.
Social responsibility.
A major enhancement implanted by the company in 2018 was the creation of the supplier performance management process. In this process, a group of suppliers receives performance indicators on a monthly basis. If they are unable to meet the stipulated targets, suppliers may contact a dedicated Avibras team.
Suppliers who do not achieve their targets are requested to formulate an action plan which is monitored by the Avibras’ supply chain, quality and engineering teams. The objective is to address the root cause of any such failure and to improve results.
One of the company’s challenges is to maintain all the dimensions of quality as a priority. This encompasses product and service performance, reliability, conformance, durability, customer service, as well as technical and aesthetic characteristics, being designed to guarantee the perception of quality by Avibras clients.
Quality is a theme which the company will work on in the first six months of 2019. The work fronts to be developed are clients, continuous improvement and processes, personnel development, partnerships with suppliers and elevating the level of the quality management system.
The actions are based on three factors: suppliers conference, performance indicator management and action plan management. They involve the application of quality, quantity and punctuality metrics, with the objective of establishing supply, evaluation and qualification contracts with the company’s suppliers.
The goals established for 2019 include the implantation of a supplier risk management process, improvements to the supplier performance management process, increasing the number of companies participating in this process, as well as the implantation of a Supplier Portal to improve management and communication between the parties.
The company provides orientation for its supplier base by means of the Supplier Manual, the Avibras Code of Conduct, the supplier qualification audits, and management of the action plans applied to each supplier. Terms of commitment are included in all purchase orders and supply contracts. 205-2
Avibras does not do business with partners, agents and contractors who do not adopt a zero tolerance approach to corruption. All company contracts contain anti-corruption clauses.